Residential Projects
Buxton Point Builder Bets on Tech to Quicken Work
GulfCap Real Estate is using tunnel formwork to expedite projects.
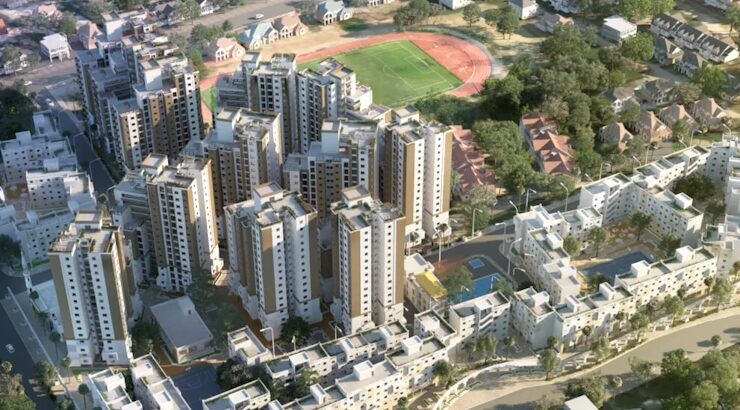
GulfCap Real Estate has adopted tunnel formwork technology in its mega construction sites as it seeks to deliver over 7,000 houses in less than three years.
The company is developing Buxton Point estate in Mombasa and Starehe Point estate in Nairobi – with valuations of Sh6 billion and Sh20 billion, respectively.
GulfCap Real Estate has acquired the technology from its partners in India, China, and Turkey to deliver the government-backed mass affordable housing scheme.
Its chief executive, Chris Ochieng, says adopting formwork technology is one of the ways of enhancing efficiency and raising the quality of projects.
“With a target of delivering over 7,000 units in less than three years, it’s no longer feasible to deliver those units using the traditional brick and mortar methodology, hence the need to incorporate technology in our construction,” Mr Ochieng said.
Tunnel formwork
Tunnel formwork is a technique that allows the casting of walls and slabs in one operation, resulting in a cellular RCC (reinforced concrete cement) structure.
It combines speed, quality, and precision while offering the adaptability and cost-effectiveness of on-site construction. The formwork, typically made of steel or fiberglass, serves as a mould for casting walls and slabs simultaneously.
RELATED: Inside Mombasa’s Sh19bn Affordable Housing Project
Site crews assemble the formwork into a tunnel-like structure, where concrete is poured into the mould, creating walls and floors seamlessly in a single operation.
The speed of tunnel formwork arises from its ability to construct entire sections of a building at once, reducing the need for time-consuming, sequential processes.
This strategy, Mr Ochieng says, will ensure completion of the structures within a year and a maximum of 18 months for new homeowners to occupy their homes.
“We are on course to deliver Buxton Point Phase 2 by the fourth of 2025. The integration of the tunnel formwork system positions us to achieve unprecedented efficiency and quality standards in affordable housing construction,” he said.
Phase 2 of Buxton Point estate, which kicked off shortly after the handover of phase one to the owners in September last year, involves the construction of 16-storey towers that will hold an additional 1,400 units.
FAQs
What is the tunnel formwork method?
Tunnel formwork is one such process whereby the walls and slabs are cast in one operation, consequently giving a cellular RCC structure.
This technique brings together the characteristics of speed, quality, and accuracy with the flexibility and affordability of on-site building.
What are the advantages of tunnel formwork?
It accelerates construction through the concurrent casting of walls and slabs, by simplifying steps. Hence, it is suitable for repetitive structures because it possesses the cost-effective feature of reusability for quick, efficient, and homogeneous construction of buildings.
What are the disadvantages of tunnel formwork?
Although it is quite efficient in structures of a repetitive nature, tunnel formwork does have limits to its adaptation to unique designs.
Besides, it may not be suitable for minor projects due to the comparatively higher investment costs, and it is pretty flexible when architectural requirements are complicated.
