Residential Projects
World’s First ‘Carbon Concrete’ House Underway in Germany
Carbon concrete is lighter and stronger than regular concrete.
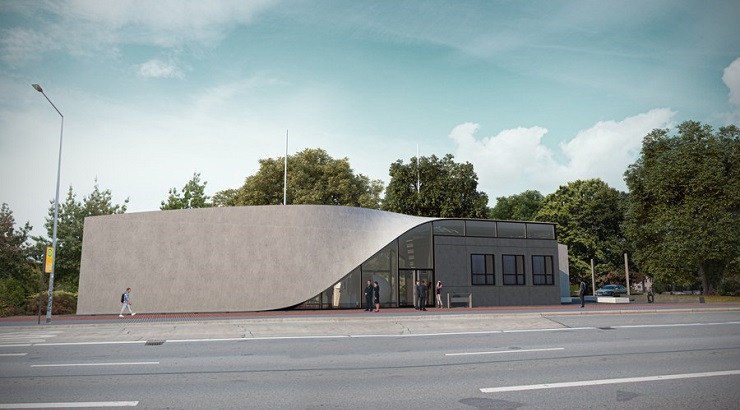
Scientists at the Technical University in Germany have teamed up with architecture firm Henn to create the first concrete building to be reinforced with carbon fibre instead of steel.
Currently under construction at the university’s Dresden campus, the house – which is known as The Cube – is being marketed as the world’s first building made of carbon concrete.
The Cube, which has a floor area of 220 sq. m, will be used as a meeting and exhibition centre. The project is financed by Germany’s Ministry of Education and Research.
It is a showcase project of the “C³ – Carbon Concrete Composite” research initiative.
According to the researchers, carbon concrete is four times stronger than regular concrete and four times lighter thanks to the reduced structural sections.
The wonder material allows slimmer and more flexible designs.
The concrete is reinforced with carbon fibre yarn, which is made by fusing many carbon fibres – ultra-thin threads of pure carbon crystals – in a thermal decomposition procedure known as pyrolysis.
Immune from Corrosion
The carbon fibre yarns are used to make a mesh into which the concrete is then poured. This mesh is immune from corrosion, unlike steel, which gives carbon concrete a longer lifespan.
RELATED: The World’s Most Beautiful 3D Printed Homes
With a wall that folds up to become a roof, The Cube’s design is inspired by the lightweight and flexible properties of carbon fibre.
“[It suggests] a future architecture where environmentally conscious design is paired with formal freedom and radical rethinking of the most basic architectural elements”, Henn said.
The company added that switching to carbon concrete could reduce the carbon emissions from construction by up to 50 per cent.
However, environmentalists like Dr. Erik Frank, who heads carbon fiber development at the German Institutes of Textile and Fiber Research, are particularly concerned about the carbon footprint of carbon concrete.
“[Lignin] is a waste by-product which accumulates in the paper industry. Normally, this is added to concrete or asphalt or incinerated. We are using it to make carbon fibre,” he said.
Carbon fibre is widely used in the manufacture of aircraft, as well as high-performance products such as cars and wind turbines. Thanks to its extreme lightweight, the material can significantly improve performance while reducing energy requirements.
However, in addition to the high cost of production, carbon fibre is not sustainable enough to become the standard for the construction industry – which is increasingly looking at doing things more sustainably.
How to Make Concrete Fibre
Carbon concrete is manufactured in three different processes:
- Carbon fibres are added to concrete and distributed throughout the building component.
- Grid-like textile mats made of carbon fibres are placed between fine concrete layers.
- The fibres are sprayed into the concrete – creating concrete with high tensile strength.
