Outdoor Living
3 Types of Flat Roof Houses
Everything you need to know about a flat roof.
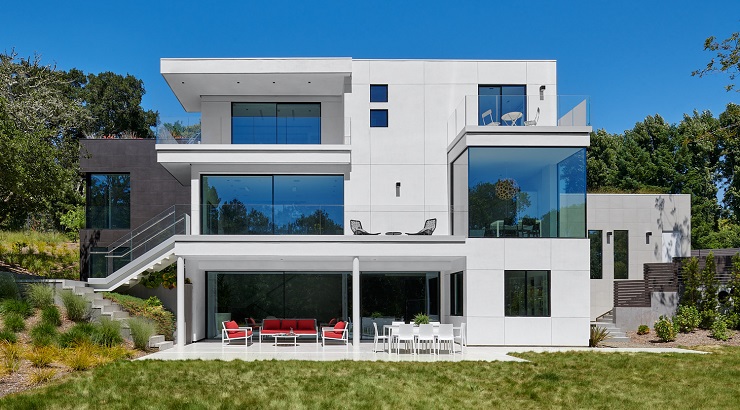
Flat-roof houses are increasingly popular with modern builders due to their gorgeous looks. However, the roofs that are inspired by ancient Arabian architecture are infamous for leaks and costly repairs.
Here is what it takes to build a flat roof that does not leak; including the materials, tiles, skylights, and what to do and not to do when repairing a flat roof.
What is a flat-roof house?
A flat roof is an almost horizontal rooftop, with only a slight slope of between 1/4″ to 1/2″ per foot (up to 10 degrees) – enough to drain water if fitted properly.
However, flat roofs can hold snow and water for longer durations compared to the standard pitched roofs hence they require special types of materials to remain waterproof.
A properly installed flat roof can last 20-25 years with regular maintenance.
Materials
There are three main categories of flat roofs based on material types.
- Built-Up Roof
- Modified Bitumen Roof
- Membrane (Single-Ply) Roof
Each of the above options has its advantages and disadvantages that should be considered before embarking on a flat roof installation project.
Built-Up roof
Built-up roof membranes (BUR) were the flat roof material of choice for builders in the early 1900s before the advent of modified bitumen and membrane roofing systems.
It consists of several layers of material: a bottom layer of insulation board, several middle layers of bitumen alternated with layers of reinforced fabrics (roofing felt, or ply sheets), and a top layer of gravel.
The bitumen mostly used in built-up roof systems is asphalt, cold-applied adhesive, or coal tar.
The hot-applied tar mixes with the bitumen-saturated reinforcing fabric to create a monolithic roof membrane. The roofing felt is applied in overlapping layers until the assembly is two or four plies thick.
RELATED: 27 Popular Roofing Designs
BUR is considered to be adhered if applied directly to roof decks or insulation.
Surfacing for built-up roofs includes mineral surfaced cap sheets, aggregate, hot asphalt mopped over the entire surface, elastomeric coatings, aluminium coatings, or glass fibre.
Pros
- BUR offers excellent protection against fire.
- It is the cheapest of all flat roof varieties.
- It costs little to maintain throughout its lifecycle.
- Layers can be removed when repairing the roof.
Cons
- BUR installation is a labour-intensive task.
- It is very heavy and often requires reinforcement of the roof deck before installation.
- Dangerous fumes are emitted during installation.
- It is difficult to identify and fix leaks.
- Loose gravel can choke gutters and scuppers.
- It is not flexible in cold weather, making it prone to damage.
Modified bitumen roof
Modified bitumen roofing (MBR) is asphalt-based sheet roofing that was developed in Europe in the mid-1960s as a lighter alternative to BUR. It is designed for buildings with low-slope roof structures.
It is designed using built-up roofing technology, with manufacturers adding polymer-reinforced roof wear layers or rolled sheets to give builders a wider array of options compared to the BUR systems.
The rolled sheets are usually 3 feet wide and up to 36 feet long and are rolled onto the roof over a base sheet membrane.
Modified bitumen roofing may be fitted using the torch-application method, which involves heating the bottom of the roofing sheet as it is unfolded to melt the material to the bottom layer.
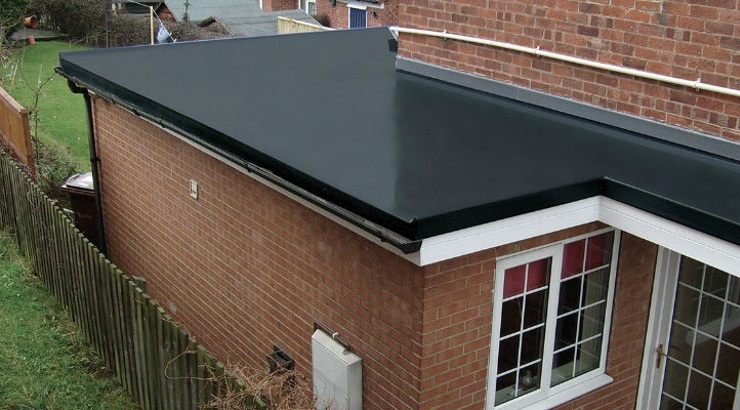
There are versions of MBR that come with a self-adhering sheet. Using polymers to modify the bottom of the modified bitumen sheet, manufacturers deliver rolls that are fitted with release papers.
Once the installer removes the release paper, the sheet rolls out and adheres itself to the substrate – thus eliminating the risks that come with the usage of hot asphalt, and torches.
In addition to the ease of application, the modified bitumen sheet is free of VOC (volatile organic chemicals) gases during and after application.
Pros
- MBR is easier to install compared to Built-up roof membranes.
- Self-adhesive roll sheet can be a DIY installation task.
- It offers flexibility at low temperatures.
- MBR is low-maintenance and durable.
- Most of MBR material can be recycled.
Cons
- The torch-down application can cause a fire if done by an amateur.
- MBR is the least attractive of all flat roof varieties.
- Overlapping joints can cause leakages if not properly adhered to.
- They are prone to scuffs and tears.
Membrane (single-ply) roof
Technically known as plastomeric or elastomeric roof membrane, the single-layer roof is the latest roofing technology and the material of choice for commercial buildings – most of which are fitted with flat roofs.
As the name suggests, single-layer roofs (also branded as single-ply roofs) are designed to be installed in one layer. They are generally categorised into two clusters: thermoplastics and thermosets.
Thermoplastic membranes are generally designed to include a reinforcement layer, normally polyester or fiberglass that offers supplementary strength and stability. They are ideal for large roof areas since their manufacturing size is optimised for reducing or minimizing seams.
RELATED: How to Choose the Best Roofing for Your Home
On the other hand, thermoset membranes are made from synthetic rubber polymers, the most common being EPDM (ethylene propylene diene monomer), which is also commonly used as a pond liner.
Both thermoplastics and thermoset membranes are very flexible and resistant to ultraviolet radiation.
Single-layer membrane roofs are installed as thin sheets – 30mm to 60mm – thick and are applied to the roof in a single layer. They are flexible and can withstand temperature changes better than built-up roofs.
Pros
- EPDM roofing is lightweight and does not require reinforcement of the roof deck.
- The roofing material is highly resistant to scuffs and tears.
- EPDM retains enough heat to cut a home’s heating bills.
- EPDM roofing does not leak easily unless surface damage occurs.
- Leaks are easily repaired.
Cons
- It is the most expensive of all flat roof varieties.
- It is easily punctured by foot traffic during maintenance leading to leaks.
- Chimneys and other roof penetrations make installation difficult.
- Joints between membrane sheets are prone to leaks.
Tiles
As the demand for outdoor entertainment spaces continues to rise, homeowners in urban areas are increasingly turning their rooftops into open-air living areas.
Instead of using the above roofing systems, homeowners are erecting concrete roofs and fitting them with tiles that can emulate the texture of other flooring materials such as wood, marble or granite.
Unlike other floor coverings, tiles for flat roofs must be UV and weather-resistant.
Some of the popular tile options include rubber, perforated PVC, wood tiles or simulated grass – an artificial grass top that is designed to feel soft on bare feet.
Skylights
Skylights are roof openings that are fitted with glass to admit natural light into a room. Unknown to many people, a flat roof can also be fitted with a skylight but this has to be done by a professional.
Skylights for flat roofs must be fitted in a sloping manner for easier drainage of rainwater. Without slanting a skylight, rainwater will collect and form a pool on the glass. This becomes a problem even after the water evaporates as it leaves ugly marks and stains.
Skylights must be installed properly as they can cause leaks, especially on a flat roof.
Repair
Repairing a flat roof is a complex task. Depending on the type of roofing system, flat roof repair can range from a simple fix to an intricate repair that requires the removal of the entire roof.
As such, even if you can identify the cause of leaks by yourself, it is important to call the contractor who installed the roof for repairs. If this is impossible, try and look for experienced professional support.
