Industry News
Builders Hit Hard by Steep Rise in Cost of Materials
Developers are also facing a shortage of key raw materials.
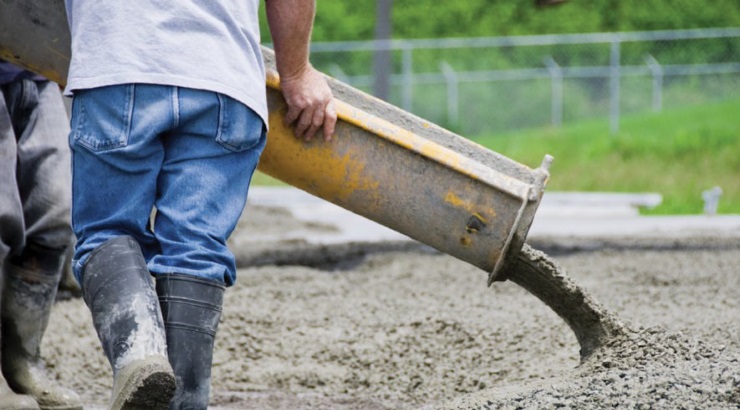
A steep rise in the prices of building materials has worsened the financial woes of builders who are still grappling with the adverse effects of the Covid 19 pandemic.
Prices of materials such as cement and steel have hit the roof over the past six months, causing concerns among construction managers who are worried about the additional costs they have to incur to keep their sites open.
According to industry sources, prices of steel bars have risen by between 80% and 90% in six months. For example, D8 which cost Sh460 in October now retails at Sh830. On the other hand, D10 is now selling at Sh1, 280 up from Sh660.
The prices of steel have shot up over the past three weeks on supply worries related to the Russia-Ukraine war, with the conflict and ensuing Western sanctions raising disruption fears.
Russia is the world’s fourth-largest steel exporter, serving over 150 countries and territories. This means any supply disruption will have a damaging impact on the construction industry.
Since the beginning of this month, every week has seen an upward push in prices across steel products – escalating construction costs in Kenya for builders.
RELATED: Tough Times for Builders as Steel Prices Hit the Roof
At the same time, prices of nails and cement have risen by between 13% and 43% in the past two weeks, with a kilo of nails now going for Sh200 from Sh140 and a 50kg bag of cement retailing at Sh600 to Sh770, up from Sh530 to Sh550.
A three-metre iron sheet that cost Sh680 in November is now going for Sh800, while a two-metre sheet that cost Sh400 five months ago is now selling at Sh560 – a 40% increase.
“The abnormal spike has forced some property developers to delay awarding contracts in the hope that prices will normalise, which is affecting the delivery timeline of projects,” says John Nyaga, a Nairobi-based developer.
Paint prices have also gone up as manufacturers contend with the rising cost of raw materials and transportation costs.
Besides the rising construction costs in Kenya, local builders are also facing a shortage of raw materials due to supply disruption.
“Now because of the war in Ukraine there is a shortage of coal (and) the prices have gone up across the globe,” says Devki Group chairman Narendra Raval.
Coal is a key source of energy in cement production. It is often used to fuel high-temperature kilns that heat the raw materials of calcium carbonate, silica, iron oxide, and alumina to a partial melt at 1450°C, turning them into clinker.
According to Mr Raval, clinker manufacturing has been hit in a way that supply cannot match demand, views that have been supported by Savannah Cement managing director Samson Shivina who says there are challenges in the local production of clinker.
“This shortfall in locally produced clinker has necessitated local manufacturers to reorganise their supply chains to enable them to augment with imported clinker to address the gap in the market,” Mr Shivina said.
The rising inflationary trend of key raw materials is expected to stay in the next few months, making it difficult for developers to launch affordable housing projects since raising prices in this extremely cost-sensitive segment is difficult.
