Materials & Supplies
Logging Ban Hits Builders Hard as Costs Skyrocket
Producer prices of wood and related products rose 23 per cent – driving up consumer prices.
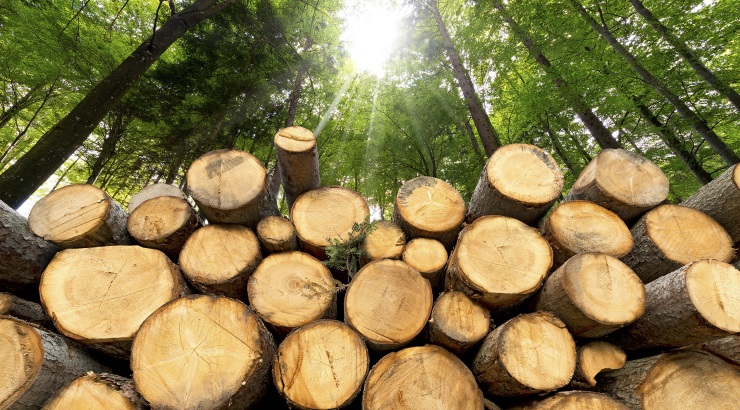
A nationwide logging ban aimed to protect Kenya’s fast-depleting forest cover has resulted in a steep increase in the prices of timber and wooden products, dealing a severe blow to builders across the country.
A quarterly Producer Price Index by the Kenya National Bureau of Statistics indicated that between March and June, the producer prices of wood and related products rose 23 per cent – driving up consumer prices.
The price upsurge coincided with a three-month ban on harvesting of trees in all private, public and community forests, which was imposed by the national government to save the country’s water towers that are facing extinction due to human activity.
The ban resulted in an escalation of prices of timber products, with the cost of wooden poles more than doubling from Sh150 a piece to about Sh320 last month due to the scarcity of the commodity.
Many builders who had already acquired poles just before the prohibition were unable to transport them to their sites since the ban included the suspension of timber and log movements.
“Some of us had stocks worth over Sh50 million in our yards and other uncollected felled logs inside forests, which are wasting away,” Timber Manufacturers Association chairman Herman Thogoto said in April.
Although the State has now lifted the ban on logging for commercial tree growers, the prices of wood products are still high due to the limited supply of the commodity.
RELATED: Reprieve for Builders as Tobiko Lifts Logging Ban
Considering that the price of sand has also hit an all-time high at a time when industry players are finding it hard to obtain credit, many builders are postponing their projects indefinitely – a situation that threatens the growth of the sector.
A Sh65 million office block at the county assembly in Wundanyi town, for example, has stalled due to a lack of wooden poles. The building is meant to house county assembly committees and members of staff.
“The current assembly is congested. It does not have public and press galleries. The assembly has 33 members. That is why we need the new building for committee and staff,” assembly clerk, Michael Ngala said.
The rising prices of timber have forced some developers to explore the use of light gauge steel trusses as a means to dodge the costs.
A steel truss is made from steel coils coated with a protective alloy of aluminium that forms a protective barrier against corrosion.
It also uses zinc for safeguarding the edges and scratches and silicon as a binding agent.
During installation or roofing, the material is cut to size and then delivered to the site in neat packs. Truss members are screw-fastened using self-tapping screws and a screw gun.
