Residential Projects
Foreign Investors Scramble for Kenya’s Prefabs Homes Market
Two overseas firms have spread their wings into Kenya in the past three months.
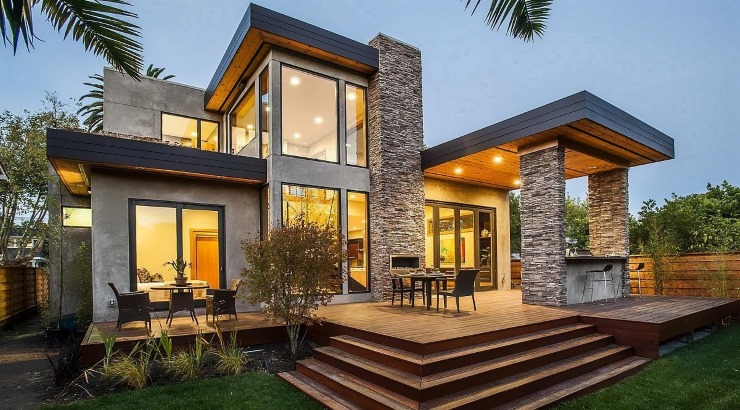
A host of foreign investors are flocking into Kenya to invest billions of shillings into prefab panel manufacturing plants to cash in on the rising demand for low-cost houses.
Two international construction firms, US-based International Green Structures (IGS) and China’s Blue Sky, have spread their technological wings into Kenya in the past three months.
IGS, which specialises in affordable housing solutions, last October unveiled a Sh851,400 two-bedroom house built using panels made from compressed rice and wheat husks targeting low-income earners.
The firm plans to build houses from prefab panels made from husks and metal frames which will slash construction time and costs by 30 per cent.
On the other hand, Blue Sky announced plans to pump Sh1 billion into a new factory in Athi River for prefabricated buildings for commercial centres, and high-rise developments such as apartments and hotels.
The company said its technology provides strength, durability, faster and cheaper construction compared to the traditional bricks and mortar — with no wastage of building materials.
In early 2014, a Malaysian firm, Koto Housing Ltd., excited the Kenyan housing sector when it announced it could build a three-bedroom house in 14 days for Sh1.8 million using prefab technology.
RELATED: US Firm Stirs Up Kenyan Market with Sh850k Homes
A similar house built in the conventional brick-and-mortar style would cost at least Sh3.6 million.
Boleyn Magic Wall Panel Ltd., a Chinese firm, has also recently unveiled a precast concrete factory in Kitengela, as it seeks to cash in on the rising demand for low-cost homes.
The factory brings into the market panels made of expanded polystyrene and precast materials to produce ‘affordable and secure’ homes.
The speed of construction could, ironically, be the technology’s undoing in Kenya – where small basic houses take at least six months to complete and where structures done fast are considered sub-standard.
However, this reasoning is unfounded as prefabricated panels are made to meet high standards of stability under extreme conditions.
Besides, before a prefab structure is certified for construction in the country it must pass stringent thermal, sound, and fire-resistance tests.
