Industry News
Builders Adopt New Technology to Cut Costs
EPS building technology slashes costs by up to 30%.
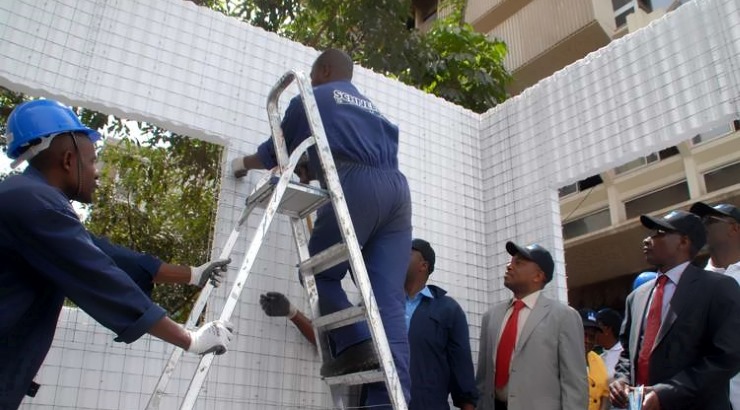
Kenyan property developers are adopting alternative building technologies in a bid to tackle rising construction costs without compromising on the quality of structures.
Among these technologies is EPS construction, which involves building houses by assembling expanded polystyrene (EPS) panels, sandwiched between a steel wire mesh that is plastered on both sides with concrete.
EPS panels, a white foam plastic material made from solid beads of polystyrene, are manufactured in a factory and transported to the site for assembly, which cuts costs by minimising the wastage of materials.
A standard two-bedroom house measuring about 100 square metres requires about 70 panels, each weighing 15 kilos – meaning a house can be carried in a single lorry load.
Construction timeline
According to Kenrick Miako, a director of Mikooh Exquisite Ltd., which has used EPS panels to build flats in Rongai, EPS building technology has helped the company to cut its costs by 25% while lowering the construction timeline by half.
“This technology cuts labour costs and construction time. The building requires less reinforcement due to its lightweight. You get further savings on the foundation as well,” Mr Miako said in a past interview.
Lightweight building panels are used to erect walls, stairways, floors, and perimeter walls.
“You use bricks only when laying the foundation. The EPS panels then take over from the walls to the slab. This results in superior structures and lends itself well to quality finishes,” he added.
Multi-storey buildings
Despite the low weight, modular houses are strong enough to withstand natural calamities, better than houses built using conventional building materials.
EPS technology can be used in the construction of up to 20 storeys.
“Buildings collapse because of self-weight. EPS is lighter. In engineering terms, we say it has a better strength-to-weight ratio compared to conventional building blocks,” Mike Juma, an engineering technologist with the National Housing Corporation (NHC) said in an interview.
A 35ml concreting of EPS panels as well as plaster finishes of 15ml on both sides of the wall results in a thickness equivalent to a 9X9 building block.
According to Juma, a storey building without columns can be as high as four floors, while a double wall panel project can be as high as 11 to 20 storeys without columns.
“However, if a building has a frame structure, the height can be infinite as EPS panels will be coming in as filler materials,” he added.
In 2011, the NHC established a factory in Mavoko, Machakos County, to manufacture EPS panels. The company has been using EPS technology in the construction of residential flats across the country.
“We have also collaborated with other private investors across the country who have adopted the technology,” he said.
Building costs
In terms of EPS building technology cost in Kenya, Juma said the panels are usually produced in different modules and variations of wall and slab panes with varying prices.
“For instance, a builder can construct a wall using EPS panels for Sh1,800 per square metre and a slab for Sh2,350 per square metre,” he said, adding that it costs about Sh600,000 to build a studio flat and about Sh1.5 million for a standard two-bedroom house.
RELATED: 7 Popular Types of Smart Building Technology
While the use of EPS panels is a relatively new building technology in Kenya, the technique has been extensively used in developed countries for many years due to its durability, lightweight, ease of installation and cost-saving benefits.
Other benefits of the technology include thermal insulation, which keeps a house cool regardless of temperature changes, as well as a high resistance to fire and other shocks.
Houses built using the EPS building technology are sound and bulletproof, and they do not attract termites, rats and other pests since the material does not have any nutritional value.
Disadvantages
One of the major disadvantages of EPS technology is that polystyrene is an oil-based product that is not easily recyclable on an industrial scale.
As such, EPS foam often ends up in nature where it is not degradable and is, instead, atomised into small parts that are harmful to humans and animals in the long run.
