Company News
Chinese Firm Opens Nairobi Wall Panels Factory
The plant targets to produce one million square metres of walling by December.
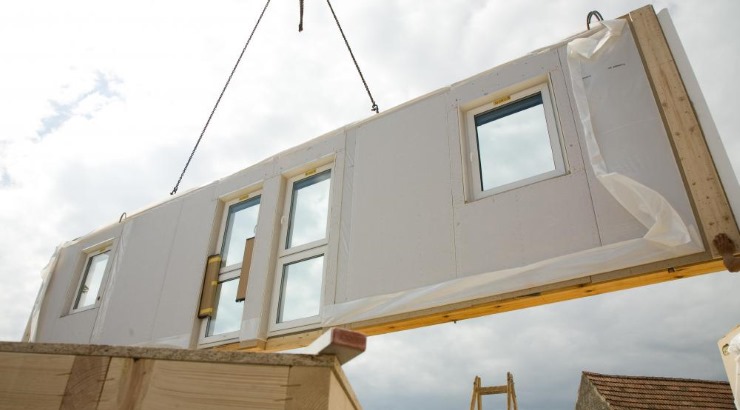
A Chinese firm has opened a wall panels factory in Nairobi to tap into the growing demand for cheaper building materials in Kenya.
Hong Kong Building Centre, founded last year, has launched operations on its Mombasa Road factory with a target of producing one million square metres of walling by December.
“We are in phase one of production and we expect to double our capacity from the current 500,000 square metres of wall panels by the end of the year,” said the firm’s owner Feng Hui.
Mr Hui, who also owns Hong Kong Ceramics, has been a key player in the local construction industry for the past 15 years. He imports mainly to retail customers although wall panels can be used in both residential and commercial buildings.
“Big companies are a bit slow because it involves a lot of consultation with the architects and contractors,” said Hui.
The firm, which is also eyeing South Sudan, joins a growing list of companies that have set up facilities to produce low-cost building materials.
One of these companies is roofing materials maker Mabati Rolling Mills, which has been supplying ready-made steel houses to its customers since August 2011.
RELATED: NHC Unveils Sh700M Prefabs Factory in Mavoko
The walls of the firm’s prefabricated houses have an option of being completed using iron sheets, wood, bricks, or mud depending on the preferences of the customer.
The National Housing Corporation (NHC) is also going big on the production of cheaper building materials. The corporation has set up a Sh1 billion factory in Machakos County to produce expanded polystyrene (EPS) panels to be used for building low-cost houses.
The EPS panels are made of insulating materials such as cement or concrete sandwiched between two wood skins and have the potential to replace brick-and-mortar construction.
Real estate players have lauded the technology saying it is the only way to counter the current housing shortage.
“It will reduce the time taken to build a house to three weeks and cut construction costs by between 20 and 45 per cent,” said James Kanyora, a property developer based in Kasarani.
Statistics show that the housing supply in the country is about 30,000 units a year against an annual demand of more than 150,000 units – leaving a deficit of 120,000 housing units.
