Innovation
Kenyan Builders Bet Big on Prefabricated Homes
Prefabricated technology could open doors for the supply of more affordable homes.
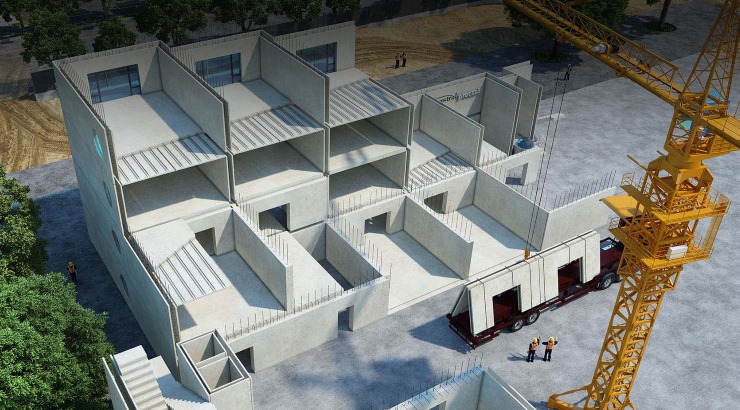
Kenyan firms are betting big on prefabricated building technology as they seek innovative ways to address the country’s housing shortage cost-effectively.
The technology involves manufacturing modular houses in a factory, usually in standard sections that can be easily transported and assembled on-site.
Prefabricated building technology lowers the overall cost of construction by up to 30 per cent while reducing construction timelines, thus opening doors for the supply of more affordable homes.
According to property analysts, prefabs could potentially be adopted on a large scale in the counties, particularly once homeowners are assured that prefabs are secure and more affordable alternatives to conventional housing.
Several companies have already shown interest in the technology by supplying prefab houses to low and middle-income Kenyans.
One such company which seems keen on revolutionising the Kenyan housing market is Koto Housing Ltd., which is leveraging on Expanded Polystyrene Styrofoam (EPS) panels to deliver cheap prefab houses.
The company caused excitement in 2014 when it announced that it could build a three-bedroom house within 14 days for Sh1.8 million (nearly half the cost) using what it called the ‘Koto Building System’.
RELATED: Build a Sleek House in Just 14 Days? It’s Possible with Koto
State-owned National Housing Corporation (NHC) has also embraced the prefab housing trend with its locally manufactured EPS panels.
The firm which manufactures EPS panels at its factory in Machakos, says the panels is capable of delivering stronger structures compared to conventional stones while cutting costs by up to 30 per cent.
A single panel – measuring 1.5m x 3.0m sells for Sh5,000 at the factory, translating to a cost of Sh1,111 per square metre, excluding transport costs and the cost of concrete plasterwork.
Roofing materials maker Mabati Rolling Mills (MRM), which joined the race for the prefabs market millions in 2011, is already cashing in on the lucrative market by supplying ready-made steel houses that retail at ‘significantly low prices’.
RELATED: Kenyan Firm Inks Sh20bn Deal for Mavoko Homes Project
In 2012, Equity Bank, for example, ventured into financing prefabricated technology with the launch of its micro mortgages product in partnership with MRM. The bank finances the cost of purchasing pre-fabricated structures from MRM.
EPCO Builders Ltd., which has been a major player in the local construction sector for the past 38 years, has unveiled several innovative building technologies, the recent being Aluminium formwork.
The technology, which is successfully used in Malaysia, Singapore, the Middle East and Japan for the construction of apartments and buildings, both low and high rises, saves on foundation slabs and reinforcements.
This is because it does not require a developer to dig deep into the ground as the materials are light in weight. Besides, Aluminium formwork gives superior walls and requires only paint as a finishing material.
“Developers who apply our technology for apartments and gated-community developments get to save over 20 per cent in the total capital injection,” says Ramji Varsani, the CEO of EPCO Builders Limited.
The acceptance of the new building technology by banks and mortgage providers is a clear indication that prefab homes will soon revolutionise the Kenyan housing market.
This is great news for a country whose annual demand for housing stands at over 200,000 units annually against a supply of 40,000 units.
