Innovation
Builders Embrace Technology to Cut Construction Costs
New technology cuts construction time-line while slashing costs by a huge margin.
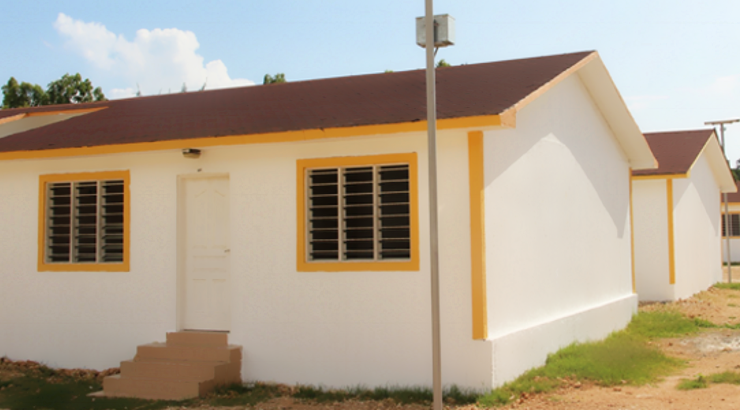
New building technology is tipped to be a game changer for the Kenyan construction industry thanks to its ability to reduce construction timelines while slashing costs by a huge margin.
Prefabrication or modular construction, now considered an essential technology to bridge the country’s house demand-supply gap, reduces construction time-line while lowering costs by up to 30 per cent.
This is because the structures, ordinarily referred to as prefabs, are manufactured in a factory in standard sections that are then transported to a construction site for assembly.
Aware of these benefits, local builders are increasingly importing innovative building technologies from Malaysia, China, Italy, and other advanced nations as they seek to boost the supply of affordable homes in Kenya.
Koto Housing Ltd., a Malaysian construction company, recently excited the Kenyan housing sector when it proclaimed that it could build a three-bedroom house within 14 days at Sh3 million using ‘Koto Building system’.
A project using this system usually starts just like a conventional building but since the wall panels are light, the foundation is not dug several metres deep.
“We use what is called a raft foundation (where the house rests on a large base [raft]), which prevents the house from cracking due to shifting of the ground,” explains Musembi Mumo, the project architect.
Once the foundation is laid, the columns are placed after which the prefab slabs are fixed into place.
RELATED: Build a House in 14 Days with Koto Building System
Elsek Construction, founded in 2001 in Istanbul Turkey, is also betting big on innovative construction technology. The firm has brought fiber cement and galvanized steel construction into the local market through its local subsidiary – Elsek & Elsek (K) Ltd.
The technology uses walls made of fibre cement boards which are bulletproof up to 9 mm and fireproof up to 800 degrees Celsius. The walls are made of cement, stone, and glue chemicals for strength and the windows are double glass or glazing for high insulation.
Elsek Group of Companies chief executive Osman Erdinc Elsek says: “Time of construction using this technology is very short. The technology utilises unwelded galvanized steel structures that act as the framework upon which covering fabric is made using fibre cement.’’
RELATED: Elsek to Provide Low-Cost Housing to Kenyans
The National Housing Corporation (NHC) is also promoting the use of EPS panels as it seeks to boost the supply of affordable homes in a country currently wrestling with an acute shortage of houses.
The state-owned company has established a prefab materials factory in Mavoko, near Nairobi, with an annual production capacity of 126,720 housing EPS panels.
Mortgage lender Housing Finance and roofing materials maker Mabati Rolling Mills have also joined the growing list of firms entering the prefab housing market.
Housing Finance said it was focusing on using pre-fabricated technology to lower house construction costs.
“We have partnerships that will see pre-fabricated panel materials come in for the construction of houses. This will make a three-bedroom house cost as low as Sh1.5 million,” said Mr David Maveke, the firm’s general manager in charge of mortgages.
RELATED: Top 5 Benefits of Prefabricated Homes
Mabati Rolling Mills will, on the other hand, supply ready-made steel houses whose walls have an option of being completed using iron sheets, wood, bricks, or mud depending on the preferences of the customer.
“The models can be custom-made for customers depending on their tastes and preferences,” said Kaushik Shah Safal, the group’s CEO for the Horn of Africa.
However, the real challenge to the uptake of the prefabs in Kenya is likely to be the “Kenyan mindset,” according to Andrew Saisi, the general manager of the NHC factory.
“Kenyans tend to think that if it’s not stone then it’s not good for building — just like the way we think that if it’s not ‘ugali’ it can’t be food,” said Mr Saisi.
Mr Saisi however believes that with a strategic focus on the rental market first, it will be easier to convince Kenyans that prefabricated houses are as good as those made using stones and bricks.
