Residential Projects
Prefab Houses in Kenya
Prefab technology allows faster construction of buildings.
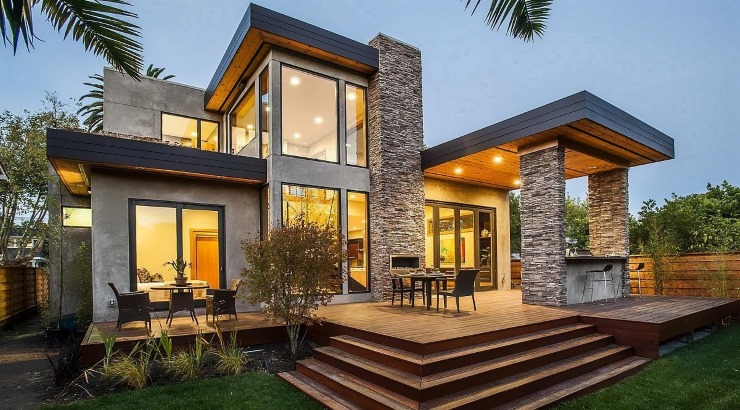
Prefabricated houses, also known as prefabs, are slowly becoming popular in Kenya as builders embrace modern technologies in a bid to dodge rising construction costs.
These houses are made using a technology that sees skeletons of buildings made in a factory before transportation to a construction site for assembly.
This technology helps to cut costs while preventing wastage of materials. It also allows faster build times – regardless of the weather – as much of the work takes place indoors.
Although prefab houses are widely accepted in developed countries, the major problem faced by dealers of prefabricated houses in Kenya is the citizens’ lack of understanding of how the technology works.
It is important, therefore, to educate the general public on how to build prefabricated houses and the benefits of prefab houses – which are arguably the future of housing in Kenya and the rest of the world.
Let’s take you through the process of making a prefabricated house.
How Prefabricated Houses Are Made
The initial process of making prefabricated houses is more or less similar to that of building a conventional home. It begins by acquiring a plot, designing the home and getting approvals.
However, a homeowner needs to contract a prefab maker to ‘build’ the house at a factory after which the parts of the house are transported to the plot for assembly.
RELATED: How to Build a House in 14 days
Homebuyers with unique designs and plans can work with an in-house architect at the prefabs factory or they can hire their architect to design their house.
Here is a step-by-step guide for building a prefabricated house.
1. Floor Assembly. The process begins by assembling the floors. A wood frame is usually placed under the floor for attachment of the wall panels.
2. Wall Panels Installation. Wall panels are attached to the floor frame with bolts and nuts. The panels are insulated and doors and windows are cut out before the panels are attached.
3. Wiring and Plumbing. Once the house structure is put in place, electrical wiring, plumbing, and drywall – including the ceiling – are installed.
4. Roofing. The roofing system can either be set on top of the walls or it can be attached to the roof on-site once the rest of the house has been assembled.
5. Finishes. Exterior and interior finishes are made, including fitting cabinets, siding, vanities and backsplashes. The interior and exterior walls are also painted.
6. Transportation. At this point, the house is moved to the owner’s plot for assembly. The transportation of the modules can be limited by the size of the road, overhangs, and powerlines.
The builders must study the route in advance to avoid getting stuck on the way.
NOTE: Before the components are moved on-site, the homeowner is expected to have excavated the land and built a foundation, which can be concrete blocks, poured concrete, basements or crawl spaces.
7. Installation. Once the modules get to the site, they should be checked for cracks and other forms of damage. After confirmation, technicians use heavy-duty cables to lift the units that come together at points known as marriage walls.
RELATED: Top 5 Benefits of Prefabricated Homes
The marriage walls bind the house together and ensure the structure is level and properly tied together. In case the roof was not set at the factory, it is installed at this point.
Thereafter, staircases, decks, and other fittings can be installed.
The delivery and installation of a house can be completed in a single day.
EPS Panels
In Kenya, the National Housing Corporation is undertaking a campaign to encourage the use of expanded polystyrene (EPS) panels in construction to boost the supply of affordable housing in the country.
EPS panels are made of polystyrene (the white material used in the packaging of electronics) and are considered favourable as building materials in terms of safety and affordability.
The state-owned company says that EPS panels can deliver stronger structures compared to conventional stones while slashing construction costs by up to 30 per cent.
RELATED: Major Boost for Affordable Housing in Kenya
The NHC manufactures EPS panels at its factory in Mavoko, Machakos County.
A single panel, which measures 1.5m x 3.0m costs Sh5,000 at the factory, translating to a cost of Sh1,111 per square metre + transport costs + cost of concrete plasterwork.
